In response to user requests, we have compiled a list of valuable tips to reduce imaging equipment down time. These tips are guaranteed to save your imaging center from extended down time, costly repairs, and the increasing cost of annual maintenance.
This article was carefully curated to contain the most important information that will save you time and possibly thousands of dollars. We encourage you to take the few minutes to read the entire article.
All of our resources will always be free. Our mission is to make a difference in patients lives by providing world-class imaging service, support and resources.
How to Minimize Imaging Equipment Down Time
We have provided 5 solutions to help you avoid unnecessary system down time and save thousands of dollars for your MRI, CT, or PET/CT Imaging System.
- How to Minimize Imaging Equipment Down Time
- 1. Reliable Air Conditioning and Chiller Can Increase Imaging System Lifespan
- 2. Save System State Routinely. Keep Multiple Copies.
- 3. Planned Maintenance Matters
- 4. Routinely Train Power On, Shutdown and Emergency Procedures
- 5. Perform Daily, Weekly, and Quarterly Image Quality Calibrations
- 6. Record and Promptly Report System Issues (Best Practices)
- 7. Take Advantage of Cost-Saving Programs!
- Conclusion
Keep your system downtime to a minimum with these helpful tips!
1. Reliable Air Conditioning and Chiller Can Increase Imaging System Lifespan
Heat and humidity are the two biggest enemies when it comes to sensitive electronics. Avoid premature hardware failure by performing preventative maintenance and regular service on air conditioning and water chiller assemblies.
Our service incident data shows air temperature along with air quality in system equipment rooms & scan rooms is a key factor in increasing imaging center efficiency. Cool, clean air will help lower the risk of premature hardware failure.
How does air quality affect my imaging center?
When assessing air quality in an imaging facility, air temperature tends to be the main focus. While air temperature is a key factor in air quality, there are some other factors to consider:
Particulate Filtration- Healthcare settings are prone to high amounts of particulates in the air. These fine, almost invisible specks end up in your system filters and settle inside system components, which could possibly lead to image artifact or functionality issues. With enough particulate and dust saturation, system filters become clogged and heat buildup begins to occur due to air flow obstructions.
- Proactive Approach: 1. Clean or replace central air conditioning unit filter regularly. 2. Clean and vacuum imaging equipment filters regularly during planned maintenance.
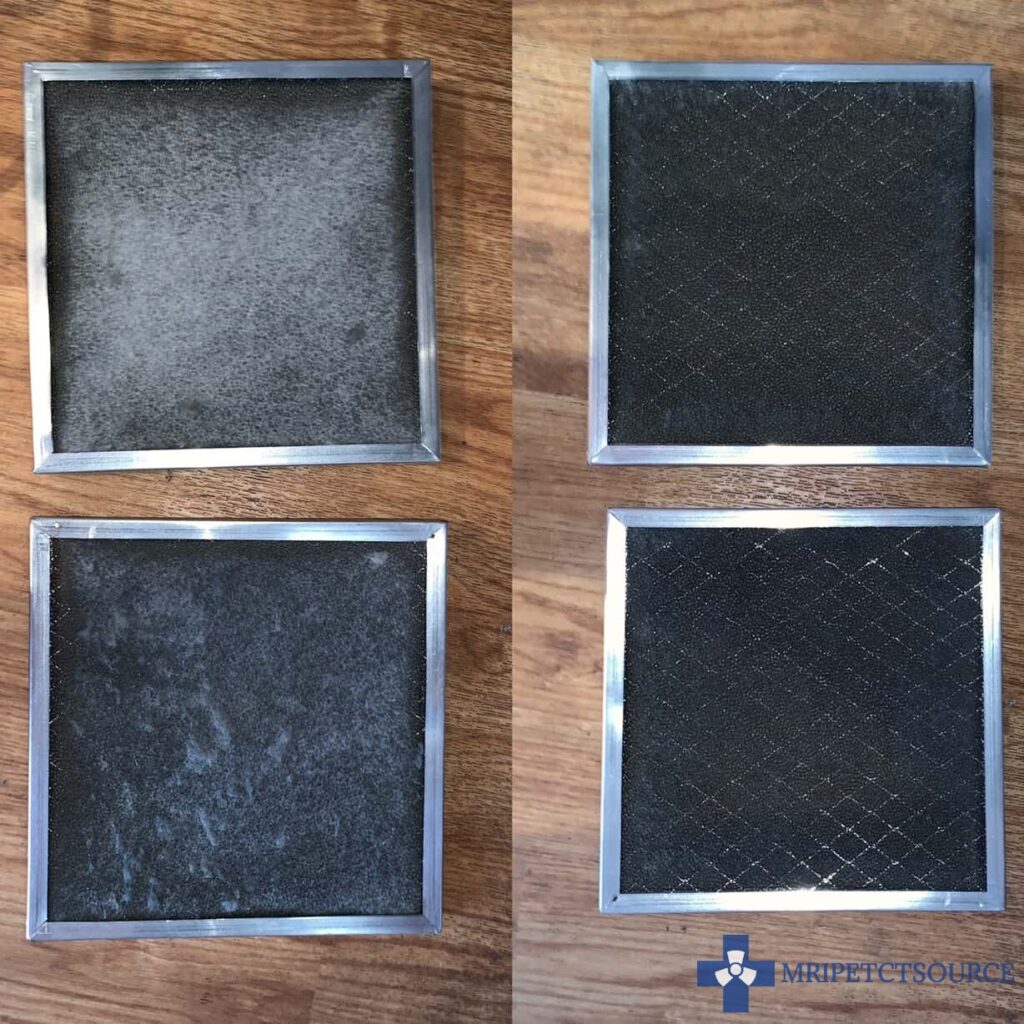
Humidity- Not only does your air conditioning system act as a temperature control, it also acts as a dehumidifier to regulate moisture in the air. Heat, humidity and obstructed air flow are the three main causes of unnecessary system failures.
- Proactive Approach: Perform routine maintenance on air conditioning units. Ensure your systems are operating at peak performance.
2. Save System State Routinely. Keep Multiple Copies.
Maintaining current saved system information files is absolutely vital to keeping your system scanning. I cannot stress the importance of saved system disks enough. They are your lifeline.
The saved system state files can be used to recover system-specific files in the event of a software or hardware failure. There is no way to recover lost system files that contain configuration and options data.
How To Save System State Files
Moreover, your system state files contain calibration files, networking values and configuration files that allow for system communication. Store multiple copies in a central location.
System configuration disks are MOD disks, CD-R, DVD-r or USB device. Consult with your Field Service Engineer for the media format your imaging system utilizes.
Losing system disks will result in unnecessary extended downtime.
System information files contain system-specific details, calibrations files and configuration settings that cannot be replaced. The absence of saved system files may result in inability to boot to applications, system configuration errors, failure to reset and system communication errors. Losing core calibration files can result in inaccurate reconstruction and distorted images.
Expert Advice:
- Keep multiple copies of saved system state files. At least 2 verified saved state media kept on-site with the imaging system.
- Keep a reserve copy in a separate room with the imaging center manager.
How often should my system state files be saved to avoid down time?
Save your system state files any time system configuration or protocol changes are made. Your field service engineer may also save system state files during planned maintenance and routine imaging equipment service.
*Always save over the oldest dated save state disk. Always label save state media with latest save date and store in a safe area.




What Happens If I Lose My Save State Media?
Losing system state media will undoubtedly result in eventual extended downtime for your diagnostic system. At minimum expect multiple days of downtime. System options, accessories and features are sold outright by original equipment manufacturer.
Recovering from a down state without system disks can be very costly to your imaging center, expect to pay up to $25,000 to recover software, configuration files and options. Expect multiple days of downtime. Avoid this scenario at all costs by taking simple preventative measures. Save system state files frequently and keep in a safe area.
3. Planned Maintenance Matters
At the most basic level, most advanced imaging systems feature components that are susceptible to dust, moisture, corrosion, and heat. Every planned maintenance visit should include a thorough cleaning of imaging systems filters. Eliminate unnecessary system down time with routine planned maintenance.
Planned maintenance will performed on bi-monthly or quarterly basis, depending on model. During PM service, all system filters will be vacuumed to avoid damage due to obstructed airflow or particulate contamination. Image quality calibrations will also be checked and corrected if necessary.
Technical documentation provides detailed outlines of tasks to be performed during planned maintenance intervals. MRI, CT, and PET/CT planned maintenance procedures typically include cleaning filters, performing image quality calibrations, performing proactive replacement procedures and quality assurance on all safety systems.
4. Routinely Train Power On, Shutdown and Emergency Procedures
Imaging system components are dependent on specific voltages, this makes MRI, CT and PET/CT Systems susceptible to hardware issues during power fluctuations. It is best practice to shutdown systems overnight or when not in use, if power incidents may occur.
System recovery after power outage, system power on procedure and proper system shutdown procedures should be curriculum in site safety and operations training rubric. A 15 minute training session with the primary service engineer will pay dividends during the next power incident. Avoid rescheduling patients and provide increased uptime with technical training.
Note: Improper shutdown of any imaging system can lead to equipment damage, injury or personnel, or death.
5. Perform Daily, Weekly, and Quarterly Image Quality Calibrations
Magnetic Resonance Imaging | Computed Tomography | Positron Emission Tomography |
---|---|---|
Routine large volume gradient shimming, geometric calibration and eddy current compensation allow for MRI to operate in dynamic environment while maintaining image quality. | Mean water levels and image quality may be affected by gradual environmental changes. Daily calibrations should be performed every 24 hours to ensure system passes ACR specifications. | Positron emission tomography utilizes ultra-sensitive detectors. Daily, weekly, quarterly and yearly calibrations must be performed to maintain optimal image quality. Consult with engineering staff. |
6. Record and Promptly Report System Issues (Best Practices)
The CT, MRI and PET/CT technologist is the most valuable asset your imaging center can utilize to avoid system down time and keep patients from rescheduling. Providing as much information to your field service engineer regarding scanning issues is the first step in streamlining your resolution.
Use a simple notebook to keep all staff and service personnel updated. This system communication log should be used to record all image quality or system issues the technologist may experience during scan operations. This helps service personnel stay up to date with the latest developments and can aid in the troubleshooting process.
When submitting a service request, additional information may be required to help expedite part orders and optimize service efficiency. It is recommended to have a site representative accessible to address any queries from the service provider.
7. Take Advantage of Cost-Saving Programs!
Increase in relief programs by OEM and Imaging Service Organizations have provided a favorable environment for imaging centers in search of cost-saving options.
- Many MRI, CT and PET/CT service companies can provide workarounds to scan issues for quick resolutions. Phone support and workarounds offer imaging systems an alternative to cancelling patients. Technical support packages can resolve up to 55% of issues within 15 minutes. It is a great resource that saves time and money.
- Demand for liquid helium is on the rise and prices have continued to follow the upward trend. The average LCC MRI consumes about 1100 liters in liquid helium per year. That equates to over $33,000 in liquid helium costs at current market value. The fact is the real emergencies involving liquid helium loss are those that occur outside normal business hours.
- Service contracts with trusted and local MRI, PET, and CT service companies is often the best and lowest cost option for equipment service and maintenance. Logistics is everything when every minute matters, so choosing the right service company from an efficiency perspective comes down to 3 factors: Engineer response time, parts availability and engineer training. Finding the right balance for the imaging center in your geographic area is key increasing year over year efficiency in your imaging center.
We have partnered with the leading diagnostic imaging service companies to provide our community members with exclusive service discounts! We negotiate special prices for our customers and provide offers that are guaranteed to benefit your imaging center.
Conclusion
These tips are sure to help your imaging center reduce operating expenses and increase imaging efficiency. Our mission is to provide the most helpful resources that help to improve the patient imaging experience.
Related resources
Join the Medical Imaging Source Community!
Subscribe To Our Newsletter To Stay Up To Date With The Latest News, Exclusive Offers, And Giveaways!
The information provided by Medical Imaging Source (“we,” “us,” or “our”) on https://www.medicalimagingsource.com (the “Site”) is for general informational purposes only. All information on the Site is provided in good faith, however we make no representation or warranty of any kind, express or implied, regarding the accuracy, adequacy, validity, reliability, availability, or completeness of any information on the Site. UNDER NO CIRCUMSTANCE SHALL WE HAVE ANY LABILITY TO YOU FOR ANY LOSS OR DAMAGE OF ANY KIND INCURRED AS A RESULT OF THE USE OF THE SITE OR RELIANCE ON ANY INFORMATION PROVIDED ON THE SITE. YOUR USE OF THE SITE AND YOUR RELIANCE ON ANY INFORMATION ON THE SITE IS SOLELY AT YOUR OWN RISK.